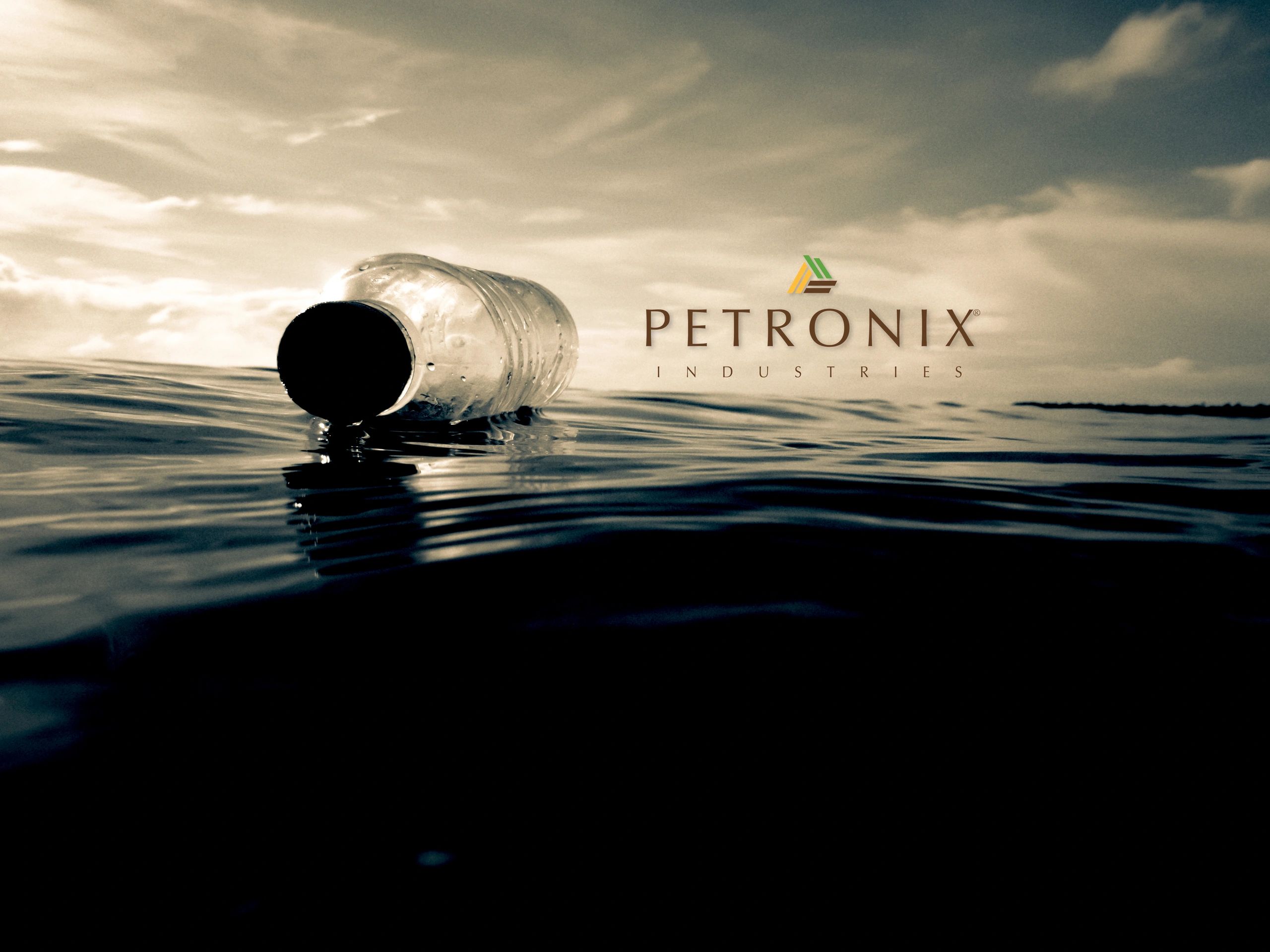
An estimated 6.3 billion tons of plastic waste had been generated as of 2015, of which only 9% was recycled. If current plastic production and waste management trends continue, 12 billion tons of plastic will be in landfills, the oceans and the natural environment by 2050.
Global plastic production was reported to be around 299 million metric tons in 2013, which significantly increased to 335 million M/T in 2016.
It has been calculated that 275 million metric tons of plastic waste was generated in 192 coastal countries in 2010, with up to 12.7 million tons entering the ocean in a single year. Following this trend, the total weight of plastic in the oceans will exceed the weight of fish by 2050!
The United Nations reported that the approximate environmental damage caused by plastic to marine ecosystems comes to approximately 15 billion US Dollars and growing exponentially!
Petronix Industries is totally committed to developing innovative and technological solutions in combating the global waste plastic crisis.
Our efforts will be coordinated along with Strategic Global Partnerships in educating countries, governments, corporations, cities, local municipalities and individuals to responsibly dispose of their plastic waste, which has been one of the largest man made disasters to date.
In addition, Petronix Industries initiative of introducing PLASTIC CREDITS to the global community will incentify everyone to play their role in responsible waste plastic disposal.
* Plastic waste MUST be been seen and treated as a realistic and viable fuel source.
* Petronix plastic waste to fuel technology utilizes plastic waste to produce high quality low emissions diesel.
* Petronix plastic waste to fuel plants produce approximately 650 -720 Liters of diesel fuel for every ton of plastic waste.
* Plastic waste is now an UNWANTED commodity globally, once traded, now currently refused by most nations.
* Demand for HIGH QUALITY & LOW SULFUR DIESEL is forecast to increase significantly from 2020 onwards.
* Petronix operating model presents a mutually beneficial opportunity to consume plastic waste and generate high returns.
* Petronix owns the rights to PYROCATALYSIS, the PATENTED process by which to produce PYRO SUPER DIESEL (PSD).
* PYRO SUPER DIESEL has a proven track record with existing clients – consuming over 1million liters per month.
* Consuming Plastic waste creates PLASTIC CREDITS - a tradable certificate used to offset plastic production.
THE HERCULES SERIES II is a completely re-designed and technologically super-charged Commercial Waste "Plastic to Fuel" Production System designed and manufactured by PETRONIX INDUSTRIES. It features clean, efficient operation, and production of high quality, low sulfur, synthetic fuel from a wide range of waste plastic. After successfully producing numerous fully functioning systems over a period of several years, Petronix Industries team of scientists and engineers broke new ground with creation of the Hercules Series II.
This model features cutting edge, industry-leading, unrivaled eco-friendly applications of Petronix Industries proprietary PYROCATALYSIS patented technology.
OPERATION
PRODUCTION SPECIFICATIONS: Production capacity of converting 25,000 kilograms of plastic into approximately 18,000 liters of Pyrolysis Super Diesel (PSD) A fully continuous, fully enclosed reactor allowing no noxious fumes to be released into the atmosphere. Non-stop“Continuous” operation, 24 hours a day, 330 days per year. Production from 25 tons plant per day is: - Diesel – 16,250 – 18,000 liters (60-65%), Naphtha – 14%, Wax – 4%, Gas – 10% (Used to fuel the combustion thru an internally connected chamber)
PRODUCTION PLANT SIZE SPECS
FEEDSTOCK: The Hercules Series II accepts most types of plastic waste. Preferred feedstock is Polyethylene (PE), Polypropylene (PP) and Polystyrene (PS) however, a combination of various types of plastics in certain feedstock, will not interfere with the production outcome.
HEATING THE REACTOR: Most traditional fuel sources can be used to initially heat the reactor depending on cost and local availability. The Hercules Series II features a closed cycle production system within which a small percentage of the various gases, heavy oil and solid by-products produced in the process, are re-channeled back to fuel the continuous combustion of the system.
ELECTRICAL POWER CONSUMPTION: 55 KW/H, or less than one KW/H of electricity per liter of fuel produced.
MANPOWER: 24-hour operation takes a workforce of 9 persons – 2-3 staffs per eight-hour shift.
SERVICE LIFE: The Hercules Series II has a longer lifespan than most systems available on the market. Minimum service life is 5 years.
TOTAL LIFE CYCLE: More than 7 years plus. A mandatory overall system maintenance is performed after 5 years.
EMISSIONS: Exhaust fumes from the furnace heating the Hercules Series II is sent through a scrubber unit before being released as excess heat which includes a small amount of CO2 and H2O. This means that the system produces extremely low or virtually no emmissions whatsoever – whether into the air, ground or waterways.
Non-Mobile Plant - Processes 25 Tons | Day of plastic waste and produces approximately 16,250 - 18,000 liters of Pyro Super Diesel (PSD) daily.
Mobile Plant - Processes 10 Tons | Day of plastic waste and produces approximately 6,500 - 7,200 liters of Pyro Super Diesel (PSD) daily.
Petronix Industries is the ONLY company in the marketplace that uses its proprietary Pyrocatalysis patented technology to process waste plastic into Pyro Super Diesel (PSD). This is a high grade petroleum which leaves zero carbon footprint in the process. This advanced Patented Pyrocatalysis Technology ensures the stability and longevity of the processed petroleum products.
Medical Waste Products.
ALARMING FACTS!
A 20 foot container being shipped from Shanghai to Hamburg emits approximately 37 kilos of sulfur. This is equivalent to 3,950 cars emissions during the same period of time.
An entire container ship at 8,000 TEU (Twenty-foot Equivalent Unit) sailing from Shanghai to Hamburg emits as much sulfur as 31.6 million cars emits during its 28 days at sea!
This means that 24 of 8000 TEU containerships emit as much sulfur as the ENTIRE WORLDWIDE FLEET OF CARS!
Before EPA began regulating sulfur in diesel, diesel fuel contained as much as 5,000 parts per million (ppm) of sulfur. EPA began regulating diesel fuel sulfur levels in 1993. Beginning in 2006, EPA began to phase-in more stringent regulations to lower the amount of sulfur in diesel fuel to 15 ppm. This fuel is known as ultra-low sulfur diesel (ULSD). EPA’s diesel standards target emissions from two different sources:
Collectively, diesel standards reduce harmful emissions from both onroad and nonroad diesel sources by more than 90%.
Ocean-going vessels and large ships traditionally used “bunker fuel” with sulfur levels as high as 5%, or 50,000 ppm, sulfur. Bunker fuel burned on these ships was a large source of harmful air pollution in the U.S.
An international treaty designated two Emission Control Areas (ECA) covering U.S. waters. The North America ECA extends 200 miles from the shores of North America, and the U.S. Caribbean Sea ECA covers waters around Puerto Rico and the U.S. Virgin Islands. The sulfur content of the fuel used in marine vessels operating in these ECAs may not exceed 0.10 weight percent (1000 ppm).
Note that a global sulfur cap of 3.50 weight percent applies outside of ECA boundaries. This limit decreases to 0.50 weight percent in 2020.
Room 1202, 12th Floor Fico Building Place 18/8 Sukhumvit 21 (Asoke) Rd, Klongtoey Nua, Wattana, Bangkok 10110 Thailand Tel: +662 005 6511
Copyright © 2019 PETRONIX INDUSTRIES - All Rights Reserved.
Powered by GoDaddy